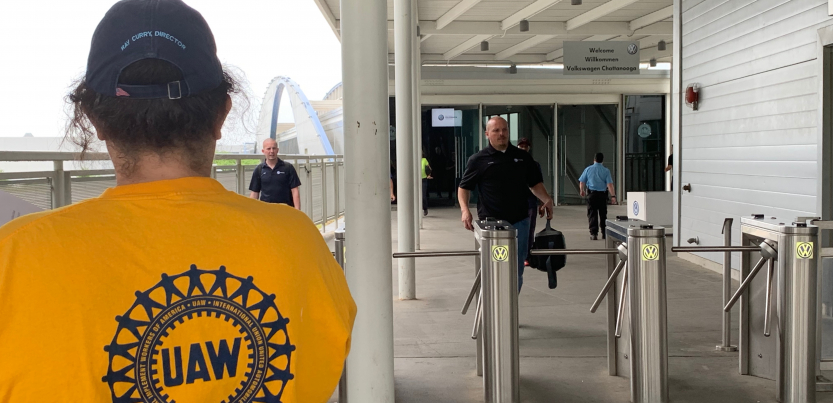
Pro-union workers leafleted at the plant gates as the election neared. Photo: Chris Brooks
“I’m only 33 and I can’t see myself working here for another 10 years,” said Ashley Murray. “I would be disabled by then. We need a union because they are a multibillion-dollar company and they treat us like shit.”
Murray is a production employee at the Volkswagen plant in Chattanooga, Tennessee, one of 18 hourly employees there I interviewed for this story. Comments like hers were almost universal.
According to these workers, on-the-job injuries are among the top issues at the sprawling plant nestled in the Appalachian mountains of East Tennessee. The union authorization election runs Wednesday through Friday this week; 1,700 workers are eligible to vote.
Many workers told variations of the same story. For the first time in their lives, they’re making good money—but they’re trapped in a job that’s chewing them up.
“My co-workers are getting hurt, I’ve been hurt, there is constant threat of injury, and if it doesn’t change, none of us will survive,” said one worker who’s been at Volkswagen for eight years but asked to remain anonymous for fear of management retaliation.
“I shouldn’t have to give Volkswagen my body in exchange for the house that I live in and the lifestyle I try to provide for my family.”
Workers described a plant where high turnover and dangerous conditions lead to serious injuries, most commonly in the hands and shoulders. Some of the workers I met now suffer from lifelong disabilities. (Click here to read one plant worker telling her own story.)
“When I went and told my supervisor I had a problem with a hand, I was called a liar. I was told I was faking,” said Daniel Maddox, who has worked at the plant for eight years. “I was told I’m a nice-sized Black guy and I should be able to deal with the pain.” He ended up having surgery for carpal tunnel syndrome.
These conditions are not unique to the German automaker. They pervade the nonunion manufacturing industry in the U.S. And to remain nonunion, companies like Volkswagen, Nissan, and Boeing have chosen to locate their production facilities in the South, where the union density is 5 percent—less than half the rate of unionization for any other region in the country.
ARE THESE GOOD JOBS?
Volkswagen was wooed to Chattanooga in 2008 with a $554 million subsidy package from the state and local governments.
It was the largest taxpayer handout ever given to a foreign-owned automaker up to that moment, and remains the largest subsidy deal in Tennessee history. The deal came free of any job or investment requirements.
“The only commitment that was made to the state was to keep the plant nonunion. It wasn’t to be safe or pay well or provide a great work environment,” said maintenance worker Gary Swafford. “It’s flabbergasting.”
The current starting wage for a production worker at the factory is $15.50 an hour and pay tops out at $23 an hour, or around $48,000 per year without overtime.
Volkswagen provides the lowest pay and benefits of any automaker in the U.S., according to a 2015 report by the Center for Automotive Research.
But there are no other automakers in low-wage Chattanooga. Wages at the plant are better than you’ll find in most local jobs that don’t require a college degree.
‘LITERALLY RUNNING’
What causes so many injuries? Workers I spoke with pointed to increasing line speeds, understaffing, and high turnover—all hallmarks of the company’s lean production model.
“They’ve cut the staffing down to bare minimums,” said production worker Drew Hall.
For instance, every line has team leads, highly experienced production workers who train new employees on the different “pitches.” A pitch is a segment of the assembly line in which a worker is responsible for performing a specific series of tasks in a set amount of time.
Team leads are not supposed to be assigned pitches of their own. That way they’re available to train new employees, step in for a worker who needs to use the bathroom, or help out if the line gets behind.
But staffing is so low that teams leads are being permanently placed into pitches on the line, Hall said.
Adding to the pressure, the company is constantly speeding up the lines, or removing a worker and redistributing the work among those who remain.
“The people who determine how much time you have in each pitch will sit there with a stopwatch and time you, and then time your downtime,” said a worker who asked to remain anonymous.
“But they don’t take into account having to grab a drink of water or having to grab tools or new materials. They will time it out so you are literally running.”
STRESSED ON PURPOSE
Workers said they’re supposed to rotate to a new job on the line every couple hours. This is supposed to help alleviate repetitive motion injuries, but it isn’t happening.
“You get stuck in the same pitches,” the same worker said. “You work eight to 10 hours a day for three days in a row and they don’t move you. The jobs are too much.”
“Some lines are still on a one-job rotation all day or all night,” said a paint shop worker. “We’ve gone from lean to starving.”
“They push, push, push,” said another worker who also asked to remain anonymous. “They overload the pitches to make the job impossible, and when you are rushing to catch up, that is when you get injured.”
Why would the company do this? “They stress the pitches to weed out the weaker team members,” the same worker said. “That’s Volkswagen in a nutshell.”
GRINDING YOU DOWN
Injuries that aren’t considered acute—if there’s no blood or broken bone—are reported to an in-plant medical team that’s notoriously dismissive.